Stainless Steel Coatings
Call 0121 236 2524 For Your Free No-Obligation Quote
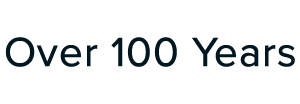
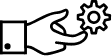


Passivation of Stainless Steel
Although referred to as “stainless”, stainless steel will show some level of corrosion over time if not treated. By passivating stainless steel any free iron on the surface is removed leaving only the non-corrosive elements of the alloy at the surface.
The MOD specify passivation of stainless steel using a nitric acid process as well as a citric acid process.
Nickel Strike of Stainless Steel
It is not possible to electroplate directly onto stainless steel as it is a very passive alloy. To overcome this a unique formulation called Nickel Strike, otherwise known as Woods Nickel, is used to deposits a thin film of nickel onto the stainless steel. Once coated with this Nickel Strike, it is then possible to electroplate in the traditional way the specified coating. This method is used so that stainless steel can be plated with Silver, Tin, Zinc Nickel alloy, Copper or Bright Nickel.
Black on Stainless
- This process is known as Stayblack and is a chemical conversion which modifies the passive oxide layer of the stainless steel leaving it matt black.
- It has many varied uses but specifically in military applications where a black, matt, non-reflective surface is essential; for example clips, aerials, latches and fixings.
- Stayblack withstands atmospheric weathering, hot water and temperatures up to 500°C without any change in appearance.
- The coating is less than 1µm thick and so will not alter any tolerance fits nor change the dimensions of the component to any significant amount.
- Stayblack does not affect the inherent corrosion resistance of the base stainless steel and will remain colour consistent longer than an untreated part.
- The surfaces can be deformed after treatment for example crimped or bent and the coating will not flake, chip or peel.
- Stayblack can be delivered either dry to touch or with a range of lubricants.
Stainless steel is a material of choice across various industries due to its durability, corrosion resistance, and aesthetic appeal.
However, to enhance its properties further, specific finishing processes like passivation and the innovative Stayblack treatment are employed.
These processes not only improve the performance and longevity of stainless steel components but also ensure they meet stringent industry standards. At EC Williams, we specialise in providing these high-quality finishing services, tailored to the unique needs of our clients across the automotive, electrical, aerospace, and other sectors.
What is Passivation of Stainless Steel?
Passivation is a crucial finishing process that enhances the natural corrosion resistance of stainless steel. While stainless steel is inherently resistant to rust, it often contains small amounts of iron on its surface, which can lead to corrosion over time. Passivation addresses this issue by removing free iron and other contaminants from the surface, creating a more stable and inert oxide layer that protects against rust and other forms of corrosion.
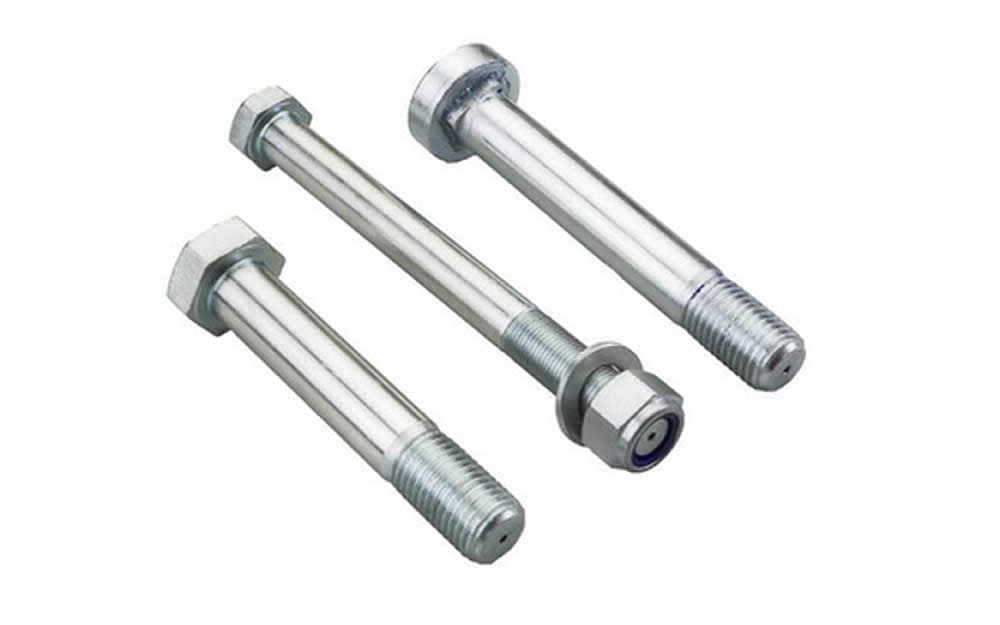
How Passivation Works
The passivation process involves several steps:
- Cleaning: The stainless steel component is first thoroughly cleaned to remove any oils, dirt, or other surface contaminants that could interfere with the passivation process.
- Acid Bath: The cleaned component is then immersed in a bath of nitric or citric acid. This acid bath dissolves the free iron particles from the surface, leaving behind a uniform and passive oxide layer.
- Neutralisation: After the acid treatment, the component is rinsed in a neutralising solution to stop the action of the acid.
- Drying: Finally, the component is dried to prevent any moisture from causing oxidation.
The result is a stainless steel surface that is more resistant to corrosion, ensuring a longer lifespan and reducing the risk of premature failure in critical applications.
Applications of Passivated Stainless Steel
Passivation is widely used in industries where the highest levels of corrosion resistance are required. Common applications include:
- Automotive Components: Passivated stainless steel is used in exhaust systems, fuel lines, and other critical automotive components where corrosion resistance is essential.
- Medical Devices: Surgical instruments, implants, and other medical devices benefit from passivation to ensure they remain sterile and corrosion-free.
- Food and Beverage Equipment: In the food processing industry, passivated stainless steel is used to prevent contamination and ensure the longevity of equipment.
Benefits of Passivation
The benefits of passivation extend beyond corrosion resistance. These include:
- Enhanced Durability: The removal of free iron and other contaminants results in a more stable and durable surface.
- Improved Aesthetics: Passivation enhances the natural shine of stainless steel, making it more visually appealing.
- Compliance with Industry Standards: Passivation ensures that stainless steel components meet stringent industry standards, such as ASTM A967 and AMS 2700.
Stayblack: The Ultimate Black Finish for Stainless Steel
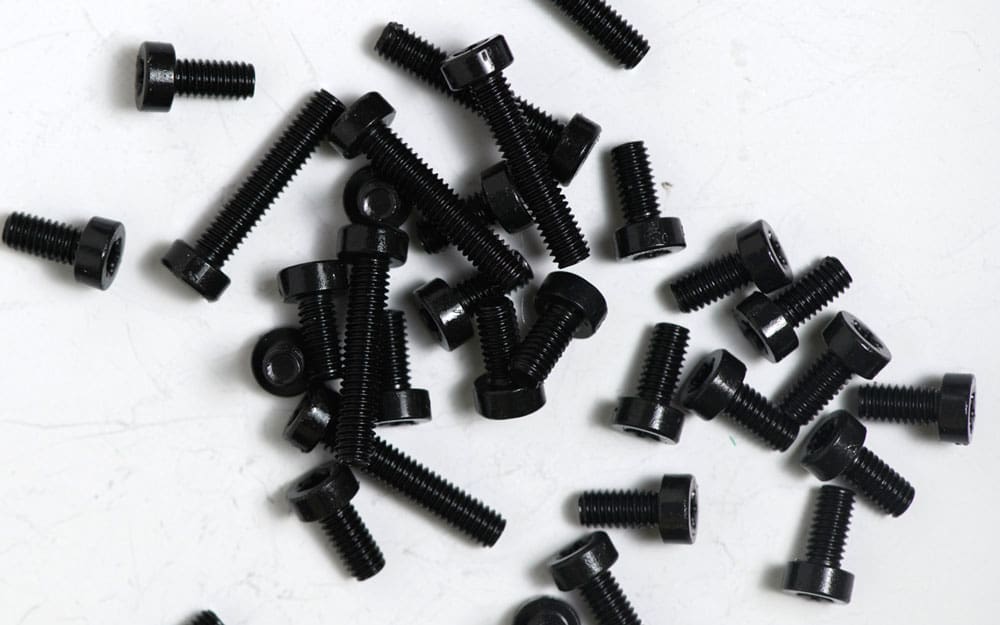
While passivation enhances the corrosion resistance of stainless steel, certain applications require a different kind of finish – one that not only protects but also provides a unique aesthetic. This is where the Stayblack process comes in. Stayblack is a chemical conversion process that modifies the passive oxide layer of stainless steel, leaving the surface with a matt black finish that is both durable and non-reflective.
How Stayblack Works
The Stayblack process involves a series of controlled chemical treatments:
- Surface Preparation: The stainless steel component is cleaned and prepared to ensure optimal adhesion of the Stayblack coating.
- Chemical Conversion: The component is then immersed in a proprietary solution that chemically alters the oxide layer on the surface of the stainless steel, resulting in a matt black finish.
- Final Treatment: Depending on the application, the component may undergo additional treatments such as the application of lubricants or sealants to enhance its performance.
The result is a uniform, black finish that is highly resistant to wear, corrosion, and environmental factors.
Applications of Stayblack
Stayblack is particularly suited for applications where both aesthetic and functional properties are important. These include:
- Military and Defence: The non-reflective, black finish is ideal for military applications, where reducing glare and visibility is crucial.
- Automotive Components: Stayblack is used for under-bonnet fasteners, trim accessories, and other components where a durable, black finish is required.
- Aerospace: In the aerospace industry, Stayblack is used for components that need to maintain their appearance and functionality under extreme conditions.
- Medical and Scientific Equipment: Stayblack is specified for components in medical, optical, and scientific equipment where a non-reflective surface is required.
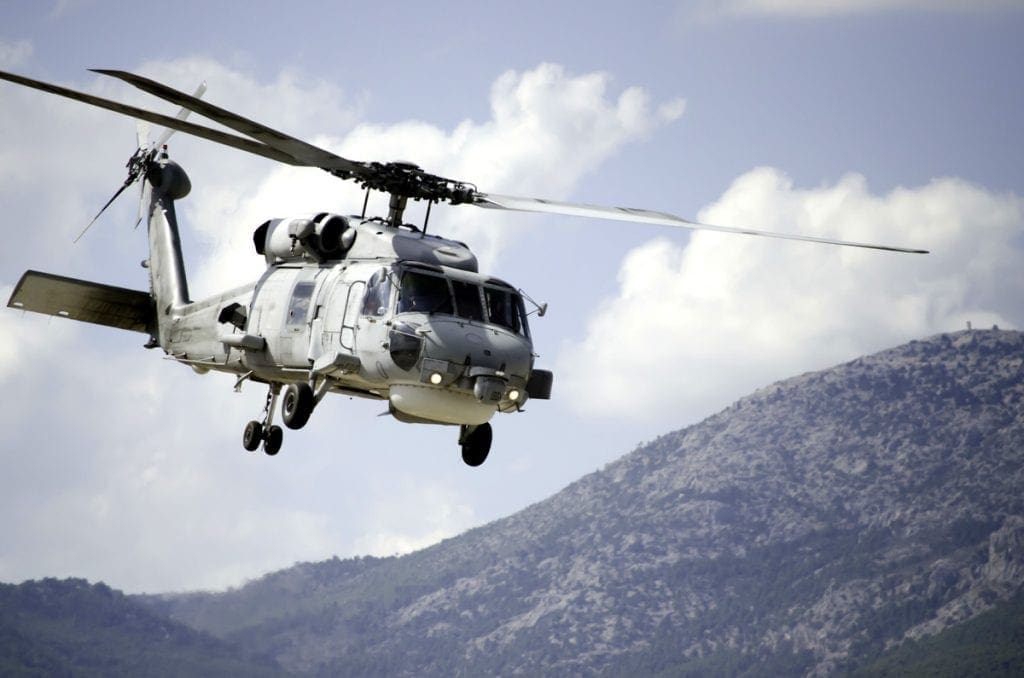
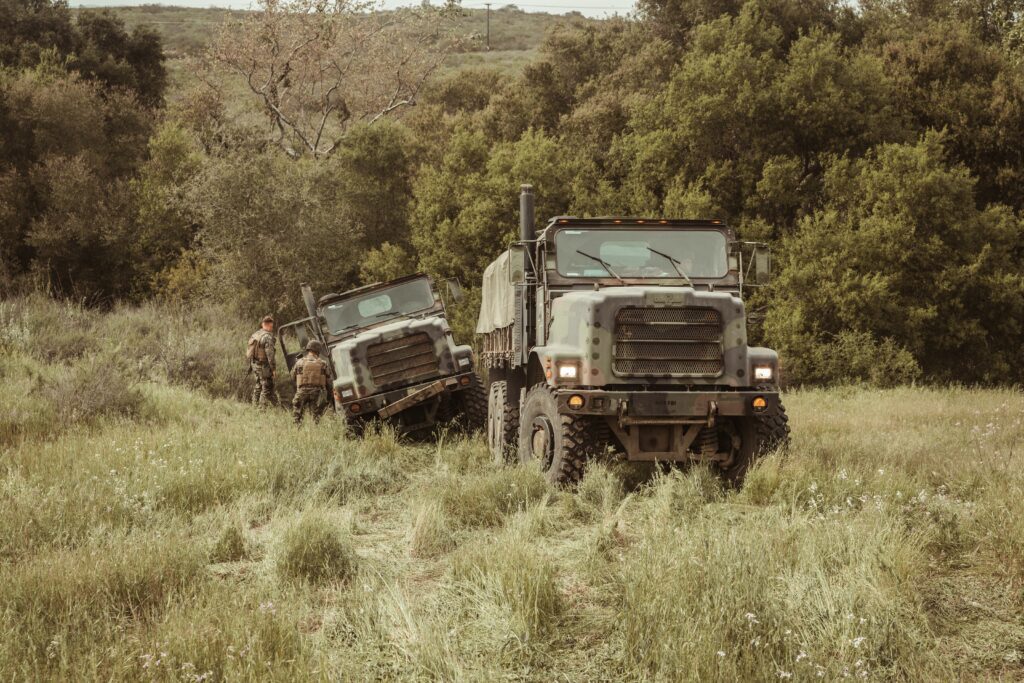
Benefits of Stayblack
The Stayblack process offers several key benefits:
- Enhanced Aesthetics: The matt black finish provides a sleek, modern look that is highly desirable in many industries.
- Superior Corrosion Resistance: Like passivation, Stayblack enhances the corrosion resistance of stainless steel, making it suitable for harsh environments.
- Durability: The Stayblack finish is highly durable, withstanding temperatures up to 500°C, atmospheric weathering, and mechanical stress without flaking, chipping, or peeling.
- Consistency: The Stayblack process ensures a uniform finish across all treated components, making it ideal for applications where consistency is critical.
Why Choose EC Williams for Stainless Steel Finishing?
At EC Williams, we bring over 90 years of expertise in electroplating and metal finishing to every project. Our state-of-the-art facilities and commitment to quality ensure that we deliver the highest standards in both passivation and Stayblack treatments. Here’s why you should choose us:
- Advanced Facilities: Our modern processing plant is equipped with the latest technology to ensure precision and consistency in every batch.
- Expert Team: Our highly trained technicians have extensive experience in stainless steel finishing, ensuring that your components meet the strictest quality standards.
- Custom Solutions: We understand that every project is unique, which is why we offer tailored solutions to meet your specific needs and requirements.
- Quality Assurance: We maintain top-notch quality standards with X-Ray Fluorescence test equipment to certify the coating thickness and alloy content of our finishes.
- Compliance: All our processes comply with industry standards, including RoHS and WEEE, ensuring that your components are not only high-performing but also environmentally responsible.
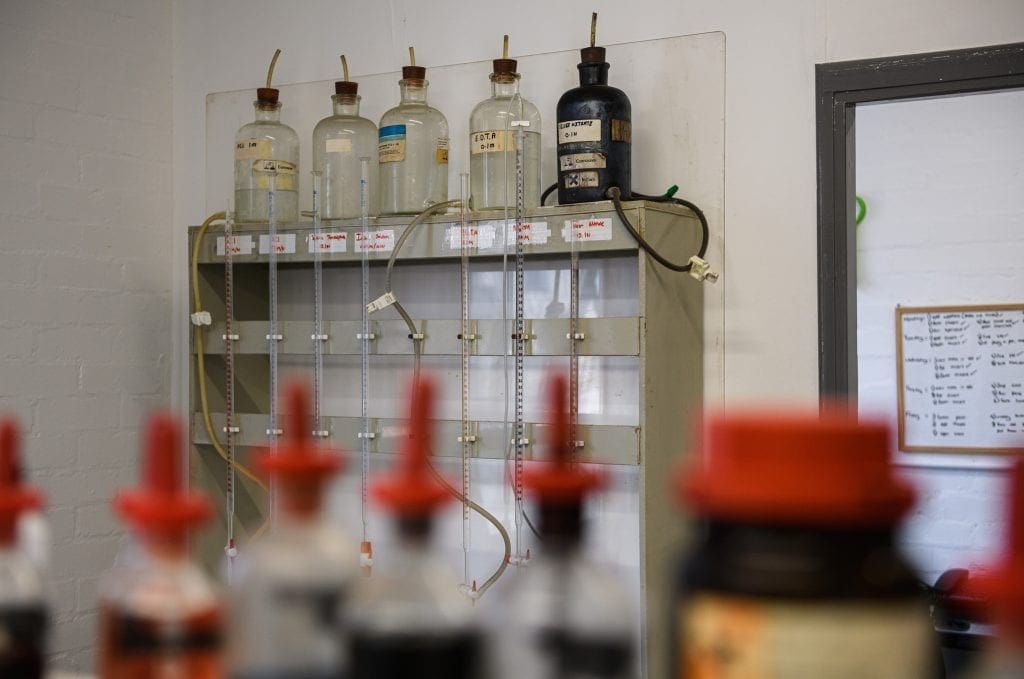
FAQs
Passivation is a chemical treatment that enhances the corrosion resistance of stainless steel by removing free iron and other contaminants from the surface. Stayblack, on the other hand, is a chemical conversion process that modifies the oxide layer of stainless steel to create a durable, matt black finish.
Yes, it is possible to first passivate a stainless steel component to enhance its corrosion resistance and then apply the Stayblack finish for additional protection and aesthetic appeal.
Industries such as automotive, aerospace, military, medical, and electrical benefit greatly from these treatments. These industries require high levels of corrosion resistance, durability, and in some cases, a specific aesthetic finish like Stayblack.
Stayblack is a superior black finish for stainless steel due to its durability, non-reflective properties, and resistance to high temperatures and environmental factors. Unlike some black coatings, Stayblack does not flake, chip, or peel, ensuring long-lasting performance.
The duration of the process depends on the size and complexity of the components being treated. At EC Williams, we aim to deliver fast turnaround times without compromising on quality.
The choice between passivation and Stayblack depends on the specific requirements of your project. If you need enhanced corrosion resistance, passivation is the ideal choice. If you require a durable, matt black finish, Stayblack is the better option. Our experts are available to discuss your needs and recommend the best solution for your application.
Conclusion
Stainless steel finishing is an essential process that enhances the performance, durability, and appearance of components across various industries. Whether you require the corrosion resistance of passivation or the unique, durable finish of Stayblack, EC Williams has the expertise, facilities, and commitment to deliver exceptional results.
With over 90 years of experience, we are your trusted partner for all your stainless steel finishing needs.
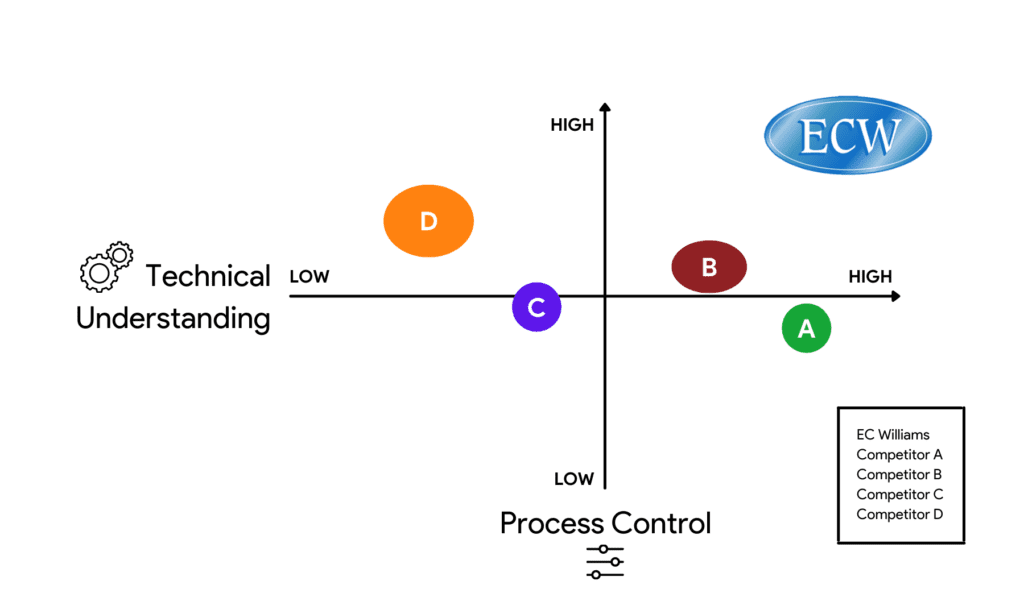
Post Plating Treatments and Quality Control
Our offerings extend to comprehensive post zinc nickel plating treatments including chromate passivates in trivalent clear and black nickel plating finishes, top coats such as silicate sealants, torque control lubricants, and de-embrittlement facilities for high tensile fasteners and springs.
We maintain top-notch quality standards with X-Ray Fluorescence test equipment certifying the coating thickness and the alloy content of the zinc nickel deposited.