Trivalent Yellow Passivate
Call 0121 236 2524 For Your Free No-Obligation Quote
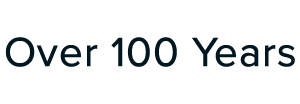
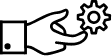


As the metal finishing industry evolves, so does our commitment to offering REACH-compliant coatings, such as Trivalent Yellow Passivate, that meet the highest standards of quality and safety.
EC Williams is proud to be at the forefront of innovative and sustainable metal plating solutions.
With over a century of expertise, we are proud to lead the transition towards environmentally friendly plating processes with our trivalent yellow and black passivates.
Yellow passivation of zinc plating has been the benchmark for corrosion resistance and cost-effectiveness for more than 100 years. Traditionally, this process involved hexavalent chromium, known for its durability and aesthetic finish. However, the environmental and health risks associated with hexavalent chromium have led to stricter regulations and the eventual banning of hexavalent passivates in commercial applications..
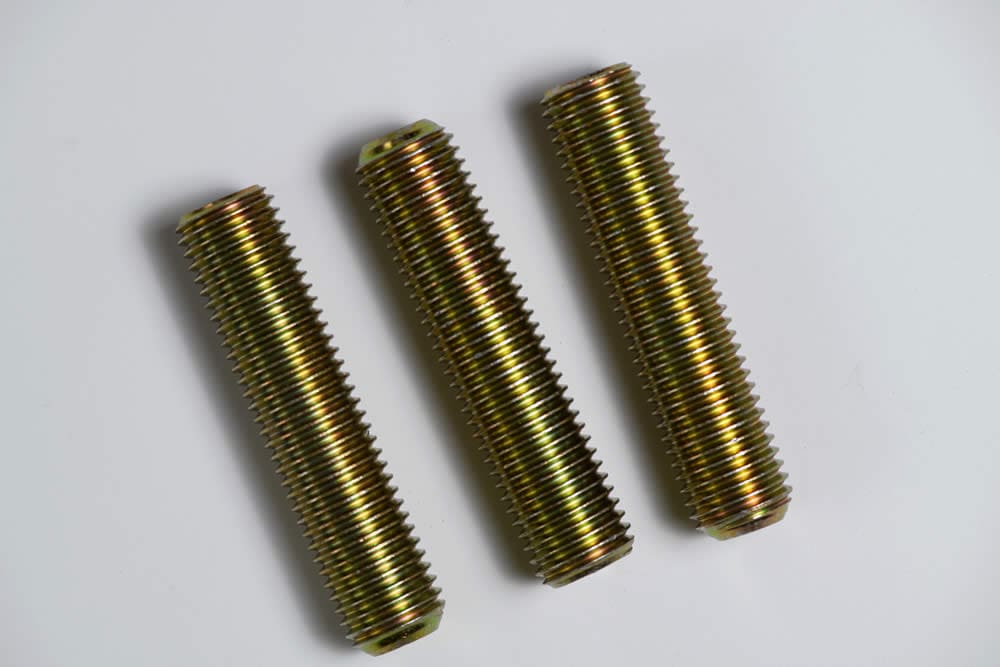
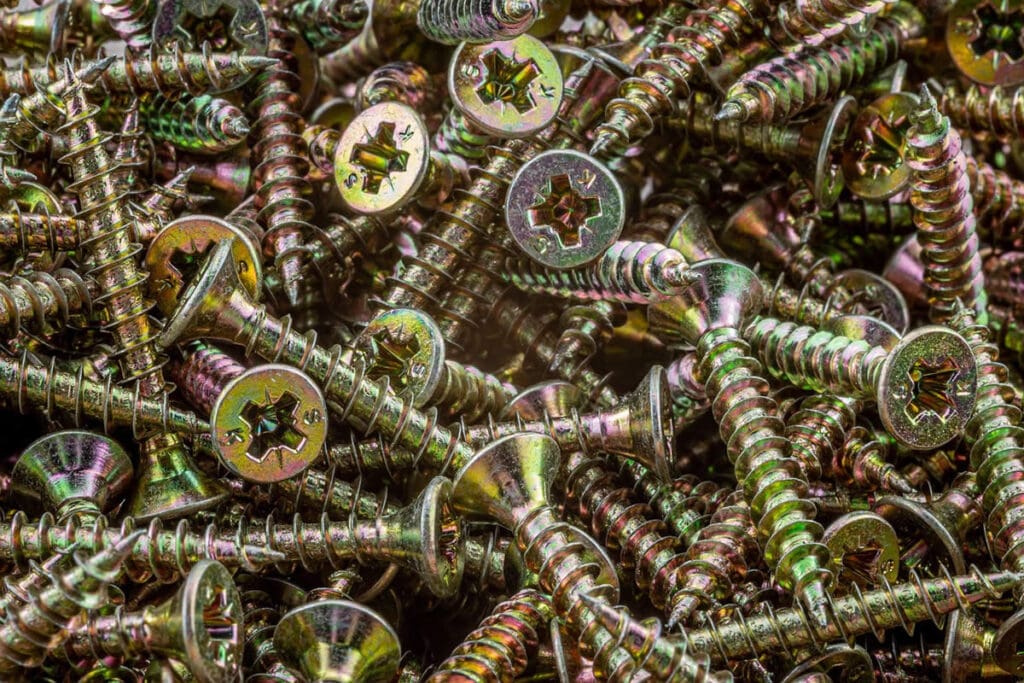
EC Williams’ Trivalent Yellow Passivate
Cost-Effective and Sustainable
Transitioning to our trivalent yellow coating provides a similar yellow coloration and comparable corrosion resistance as the traditional hexavalent coatings but without the associated health risks and regulatory burdens. This shift ensures that we continue to offer cost-effective solutions, although with a slight increase in price, the overall costs remain considerably lower than those associated with maintaining hex chrome alternatives.
REACH Compliance Without Compromise
Our new trivalent chromate conversion coating offers an optimal solution by balancing performance with environmental responsibility. It meets current REACH regulations, ensuring your business can confidently meet compliance standards without sacrificing product quality.
Benefits of Trivalent Yellow Coating
- Enhanced Corrosion Resistance: Our advanced trivalent coating technology provides robust corrosion resistance, making it an ideal choice for industries requiring high standards, such as automotive parts specified by Ford WSS-M21P17-B3 and Jaguar LandRover S437.
- Environmental and Health Advantages: Choosing our trivalent yellow passivation means opting for a coating that significantly reduces toxicological risks to workers and environmental damage. This proactive approach not only complies with but exceeds current environmental regulations, offering a sustainable alternative that doesn’t compromise on quality or durability.
Hexavalent Chromium Regulations Explained
- Hexavalent chromium is classified as a “Substance of Very High Concern” (SVHC) due to its carcinogenic properties.
- REACH regulations require authorisation for continued use from the Health & Safety Executive and the Environment Agency, a process noted for its high cost and complexity.
Our Solution:
Facing these challenges, EC Williams has proactively developed a revolutionary trivalent yellow coating. This new formulation is not listed as SVHC and is significantly less harmful to the environment. By adopting this trivalent chromium conversion coating, we are not only adhering to REACH compliance but are also reducing the ecological footprint of our operations.
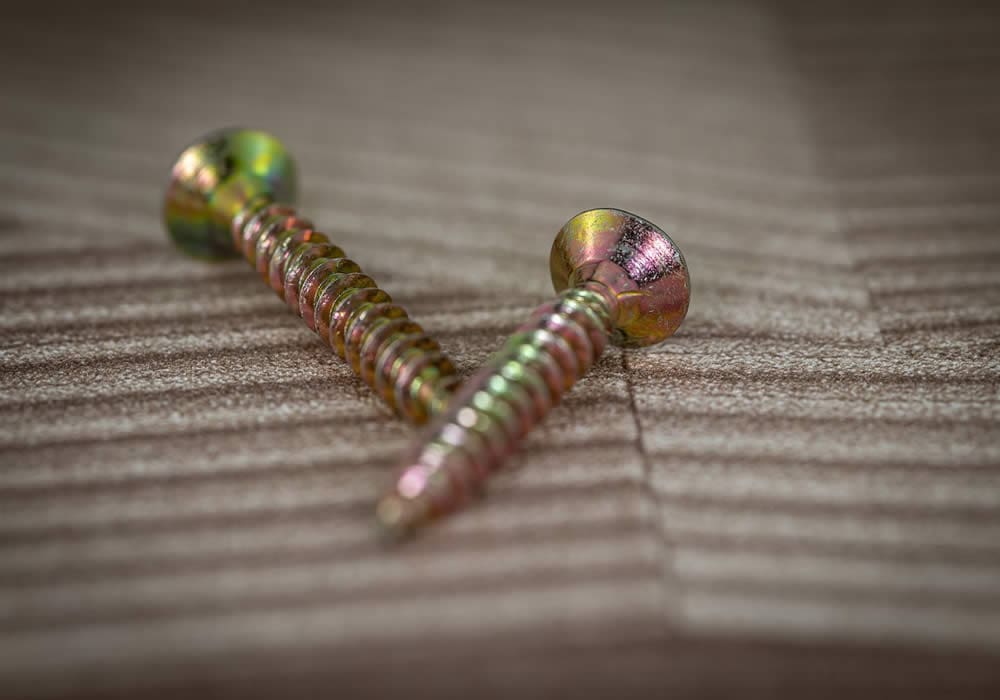
Embrace a Safer Future
Ready to transition to a safer, more sustainable metal coating solution?
Contact our experts today and learn how our trivalent yellow passivate can benefit your business.
FAQs
A safer, non-carcinogenic coating that offers excellent corrosion resistance and adherence to environmental regulations.
It eliminates the use of carcinogenic substances while maintaining high-quality standards and compliance with environmental laws.
While trivalent options might be slightly more expensive upfront, they avoid the long-term costs associated with environmental penalties and health risks.
Absolutely, our trivalent coatings meet and often exceed the specifications required by leading automotive and other high-demand industries.
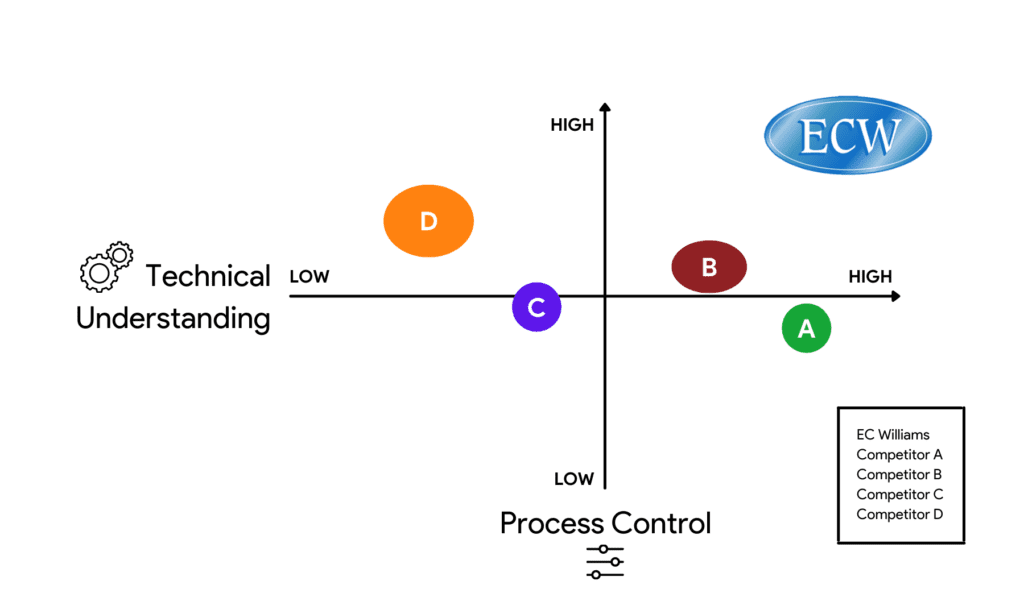
Post Plating Treatments and Quality Control
Our offerings extend to comprehensive post zinc nickel plating treatments including chromate passivates in trivalent clear and black nickel plating finishes, top coats such as silicate sealants, torque control lubricants, and de-embrittlement facilities for high tensile fasteners and springs.
We maintain top-notch quality standards with X-Ray Fluorescence test equipment certifying the coating thickness and the alloy content of the zinc nickel deposited.