Defence Electroplating
Call 0121 236 2524 For Your Free No-Obligation Quote
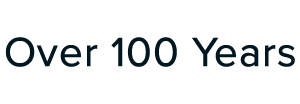
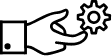


Electroplating for the Defence Sector
The defence sector electroplating incorporates many different manufacturing disciplines to supply the vast range of equipment that is needed to support the three military services. These include armaments, medical, aerospace, automotive, and electrical. All of these require components to have a surface finish applied to them.
EC Williams have been working to Ministry of Defence electroplating standards for many years and supply a range of finishes including zinc nickel alloy, tin – both matt and bright, zinc and passivation, copper and nickel.
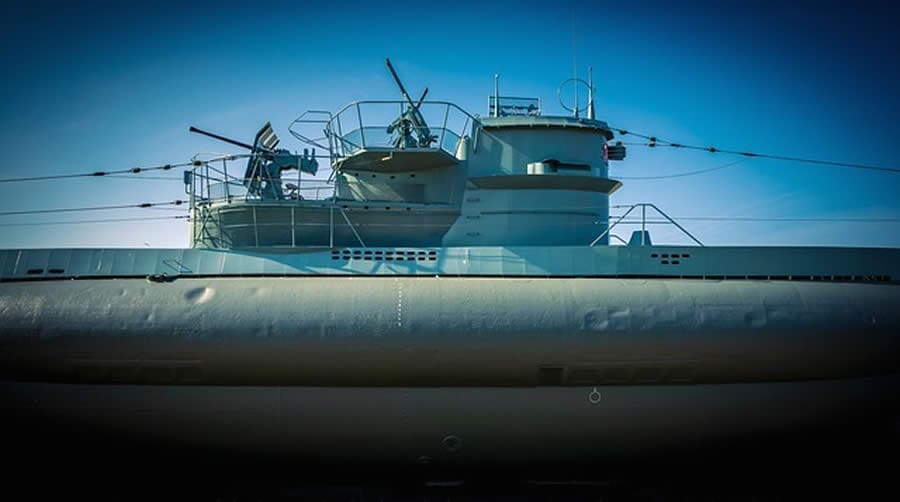
Corrosion Resistance
Military equipment is often deployed in the harshest of environments and traditionally have been coated with Cadmium to protect them. Today Zinc Nickel alloy is used, this offers a very high level of corrosion resistance while meeting strict health and safety requirements.
Bright tin plating has several applications within the defence sector.
Most commonly used in electronics and electrical equipment, its resistance to corrosion and excellent conductivity make it a solid choice for the electrical transmission and power distribution.
Traditional zinc and passivate to the defence standard DEF130 is supplied where corrosion resistance is not a priority and is often specified as an effective undercoat to subsequent painting. Additionally EC Williams supplies Copper and Nickel plating for defence components that require varying degrees of electrical conductivity or hardness.
Stayblack – The Night Scope test
At E C Williams we have been applying our black on stainless steel finish (“Stayblack”) for Defence components for many years. This is specified so that the equipment will not be visible with a night scope even though it is made of bright stainless steel.
Stayblack’s advantages include:
- Durability and stealth for components like fasteners, clips, and latches.
- Consistent matte black appearance, even in the harshest conditions.
Compliance and Quality: The EC Williams Advantage
At EC Williams, we understand the critical importance of compliance with defence sector standards. Our electroplating services are certified to ISO 9001 and ISO 14001, ensuring quality control and environmental management. We maintain full traceability throughout our processes, giving defence contractors and equipment manufacturers the assurance that their components are finished to the highest standards.
Why Choose EC Williams for Defence Electroplating?
- Decades of experience in electroplating to MoD standards.
- Proven expertise in providing Zinc Nickel, Stayblack, Passivation, and other vital finishes.
- Commitment to quality and compliance, with rigorous testing and traceability protocols.
For defence manufacturers looking to enhance the durability and performance of their components, EC Williams offers tailored electroplating solutions to meet even the most challenging requirements.
FAQs About Defence Sector Electroplating
At EC Williams, we recommend Zinc Nickel Plating for military applications due to its superior corrosion resistance, especially in harsh environments such as marine or aerospace settings. Zinc Nickel is widely used as a modern alternative to cadmium, offering excellent protection while adhering to stringent health and safety regulations.
Cadmium plating was traditionally used for its excellent corrosion resistance, but environmental and health concerns have led to its decline. Zinc Nickel Plating provides similar, if not superior, corrosion resistance while complying with current environmental regulations. It’s a safer, more sustainable solution, which is why EC Williams has adopted it as a preferred plating process for defence components.
At EC Williams, we offer a specialised black finish called Stayblack, which we apply to stainless steel components. This finish is non-reflective and ensures that equipment remains invisible to night vision devices, making it an essential feature for military operations requiring stealth.
Electroplating enhances the durability of military vehicles and aircraft by providing a corrosion-resistant surface that can withstand extreme environments, including high temperatures, humidity, and exposure to saltwater. Zinc Nickel, Nickel, and Copper are commonly used finishes that we apply at EC Williams to ensure the longevity and reliability of critical components in these sectors.
At EC Williams, our electroplating services are fully compliant with Ministry of Defence (MoD) standards and international regulations. We are certified to ISO 9001 and ISO 14001, ensuring that our plating processes meet the highest standards for quality and environmental management, which is crucial for military-grade components.
Yes, electroplating can significantly improve the electrical conductivity of components. At EC Williams, we provide Tin Plating, both matt and bright, which is commonly used in electronics and power distribution systems within military equipment. Copper plating is also used for components that require higher levels of conductivity.
Stayblack is a proprietary finish developed by EC Williams, designed to provide a durable, matte black coating on stainless steel components. This finish is critical in defence applications where non-reflective surfaces are essential, such as for fasteners, latches, and other equipment used in covert operations.
At EC Williams, we maintain strict quality control throughout the electroplating process, ensuring precise plating thicknesses and uniform coatings. Our advanced facilities and adherence to ISO standards guarantee that each component is finished to meet the specific requirements of the defence sector, ensuring both reliability and durability.
Military components must endure extreme conditions. At EC Williams, we specialise in finishes like Zinc Nickel plating, which offers high corrosion resistance in diverse environments, from desert heat to arctic cold. Our electroplating services ensure that components remain operational and protected under these challenging conditions.
Passivation is a process that removes surface contaminants from stainless steel, improving its corrosion resistance. At EC Williams, we frequently apply passivation to defence components to enhance their durability and performance, particularly in environments where even stainless steel could be vulnerable to rust. This is critical for applications like armaments, aerospace, and military vehicles.
Contact Us Today
To learn more about our defence sector electroplating services, including Zinc Nickel Plating and Stayblack,
Please contact us at 0121 236 2524 OR
Team is ready to deliver the highest quality metal finishing solutions for your defence applications.
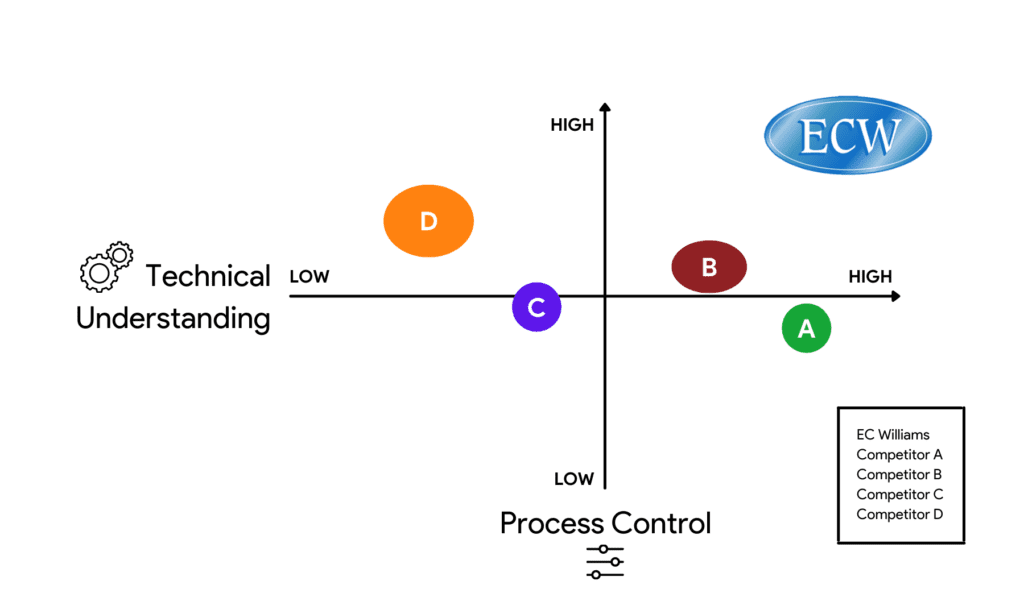
Post Plating Treatments and Quality Control
Our offerings extend to comprehensive post zinc nickel plating treatments including chromate passivates in trivalent clear and black nickel plating finishes, top coats such as silicate sealants, torque control lubricants, and de-embrittlement facilities for high tensile fasteners and springs.
We maintain top-notch quality standards with X-Ray Fluorescence test equipment certifying the coating thickness and the alloy content of the zinc nickel deposited.